Over 165 Years in Service of Excellence

The ISO 9001:2015 Certified Kiln & Dryer Company
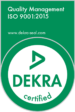
”Finch Manufacturing & Technology’s ongoing commitment to learning about, implementing and sustaining the latest manufacturing innovations relevant to their business, coupled with its dedication to product and service quality, sets the company apart from many of its competitors. Whether it’s in the performance of their ISO 9001 internal audits, the completion of Six Sigma projects, the integration of continuous improvement tools into operations or the ongoing advancement of its workforce, Finch sets the standard for what manufacturers need to do to remain competitive and provide the best products and services to existing and new customers.
Eric Joseph Esoda, CPAPresident & CEO NEPIRC
Finch Manufacturing & Technology, LLC is an ISO 9001:2015 certified company that Designs, Builds, and Installs (D-B-I) Rotary Kilns, Dryers, and other Rotary Processing Equipment (RPE). We have been operating since 1855. Our unique machinery and engineering capabilities enable us to design and fabricate the highest quality parts with precise form, fit and function to optimize your kiln. Being the only ISO 9001:2015 certified company in our industry, we take quality and customer satisfaction seriously. We offer our services at very competitive pricing.
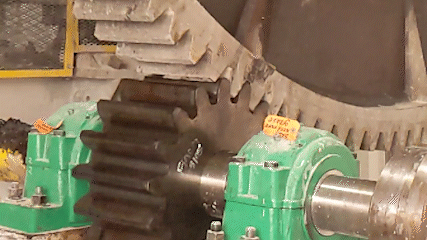
Install of New Pinion Gear
Finch is a leader in producing RPE components such as thrust rollers, trunnions, shafts, tires, drive systems, base frames, and seal systems. We have been fabricating these components for nearly 60 years at our plant in West Pittston, PA. In addition to manufacturing new equipment, we routinely refurbish thrust rollers, trunnions, and other equipment, saving our customers money. Our engineering department is often called upon to reverse engineer older or critical parts without drawings. We even remanufacture parts such as trunnions and reuse salvageable parts and save our customers 10,000’s of dollars.
Check our Gallery Section to see a good representation of the kilns and components we have designed or fabricated.
Let Finch help you increase the life cycle of your equipment (lower costs) and enhance your productivity (increase revenue). We provide extensive Field Service Support, from system inspections to grinding and alignment to component and full system installation. Our services also include installation, modification, and repair for numerous other heavy or light industries.

Dye Penetration Test on a Trunnion Head
FINCH HAS A LIBRARY OF OVER 10,000 PLUS PLANS AND DRAWINGS for Rotary Kilns, Dryers, and associated components. We have digitized these drawings to expedite the design and manufacturing processes. Many of our customers have relied on us for years, and we often receive replacement orders with little or no coordination. One customer recently asked us to manufacture a replacement for a part that we originally fabricated in 1987 and we still had the drawing! In 2019, another customer asked us to design and fabricate complex smaller specialty kilns/dryers for chemical and healthcare research. As a result, we now build kilns measured in inches to hundreds of feet and pounds to tons.

Rotary Kiln Fabrication

Rotary Dryer / Cooler Print
At Finch, we act with integrity, honor our commitments, and live in accordance with our Mission Statement:
“Provide our customers high-quality parts, equipment, and engineering services in a cost-effective & customer-focused manner that exceeds their expectations.”
Why Finch?
Tire Turning on Large Vertical Lathe (VTL)
Why work with Finch? Our record and years of experience says a lot. For over 165 years, our duty to our customers and our legacy has been uncompromising quality and a commitment to real solutions. The Finch Commitment to our Customers includes our Quality, Expertise, Purpose, Integrity, and Timeliness.
Quality
Finch offers premium-grade, durable components made of US Steel that consistently surpass industry standards in fit, form, and functionality, all at a competitive price point. We steadfastly refrain from employing off-the-shelf steel or inferior components merely to undercut pricing and secure deals, recognizing the inevitable compromise on longevity and subsequent financial burden on our customers. We proudly adhere to the stringent guidelines outlined in ISO 9001:2015, a testament to our unwavering commitment to operational excellence and quality assurance. As the only company in our industry boasting this esteemed certification, our dedication to upholding superior standards remains unrivaled in the market.
Expertise
The experience of our engineering and manufacturing team empowers us to design, fabricate, or reengineer with precision. Finch’s digitized library of drawings numbering in the tens of thousands, is a testament to our experience and expertise. If you have old or obsolete parts without drawings, reverse engineering is a standard service we offer. This capability allows us to extend your systems’ life cycle, saving capital resources. Finch provides meticulous inspections to optimize your system’s throughput and prolong its operational lifespan. We are keenly attuned to the financial implications of downtime and partner with you to proactively mitigate such costs.
Purpose
Prioritizing our customers’ needs is our guiding principle. We operate customer-centric, collaborating closely with your team to deliver tailored solutions. We maintain open communication by providing detailed quotes and weekly updates on longer projects, complete with status reports and visual documentation. We will work with you to prevent you from making the five costliest mistakes we see in our industry, including the lack of strategic preventative maintenance and not knowing how to compare quotes apples to apples for their needs.
Integrity
At Finch MT, we hold our integrity in the highest regard. We stand firm in our commitment to transparency and reliability, refusing to manipulate delivery times to win orders or secure business. Our dedication to honesty ensures that our clients can trust in the accuracy of our promises.
Timeliness
Our extensive management and operational professionalism enable us to promptly address your requirements, whether generating quotes or providing emergency services. In urgent customer’ needs, we facilitate videoconference consultations on the same day or dispatch an engineer promptly, ensuring timely resolution. We pride ourselves on being the reliable choice, as we like to say, “In a Pinch, Call Finch!”
An ISO Certified Quality Control Processes
‘Quality is job one.’ As the only ISO 9001:2015 certified company in our market, Quality Control is embedded in every step or process and part of our DNA. This commitment begins in the proposal stage and carries through to delivery. Everything is reviewed at least twice from plans, materials, and validating dimensions in the manufacturing process. Before shipping, your part undergoes thorough review and inspection by the plant supervisor and a project engineer.
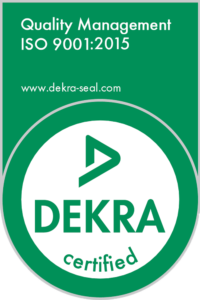
Skilled Engineering and Project Management Team
Finch’s management team possesses hundreds of years of managerial, engineering, and manufacturing experience. Our engineering and design team has a proven project management record. It can provide the full spectrum of services from designing a single part to the more complex Design-Build-Install of a rotary kiln/dryer. Our customers are assigned a Project Engineer that they will work with and take the lead on all projects so nothing is missed since they will know your team and equipment. We closely monitor all action steps with the understanding that projects have critical paths that must be managed. Every project undergoes rigorous review in our daily Engineering and Production meeting to ensure close coordination between the engineering and manufacturing teams.
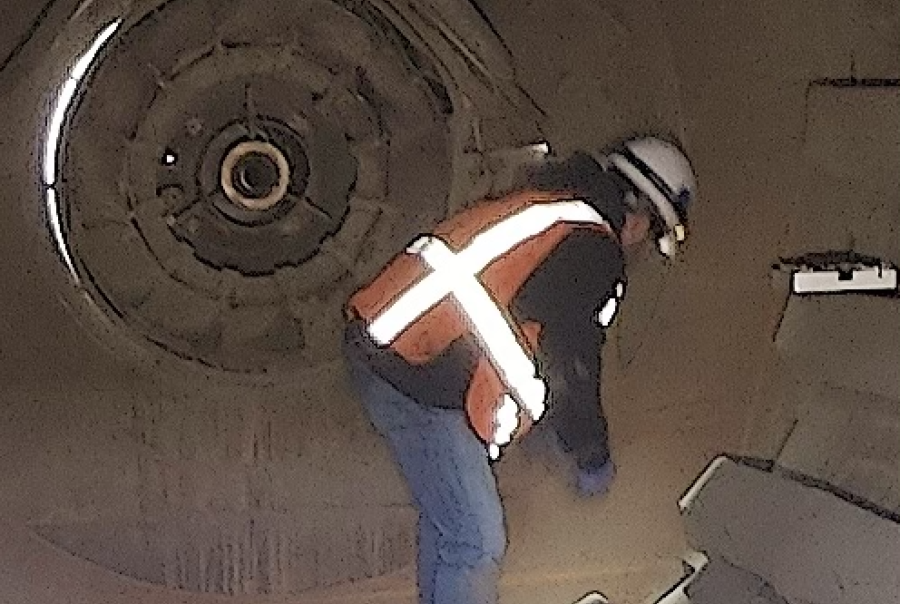
Customer-Centric Process: Customers come first
Every customer is different, but all customers expect a quality product that meets their needs in the proper form, fit and function. Our team will diagnose the problem, find the solution, and be there with you to ensure everything works seamlessly. Being present throughout the process is crucial to us. We listen attentively and ensure that both parties know the order’s what, when, and how. Some customers want constant communication, and others want to know just when their Trunnion or product will be delivered.
Unique and Flexible Manufacturing Facility
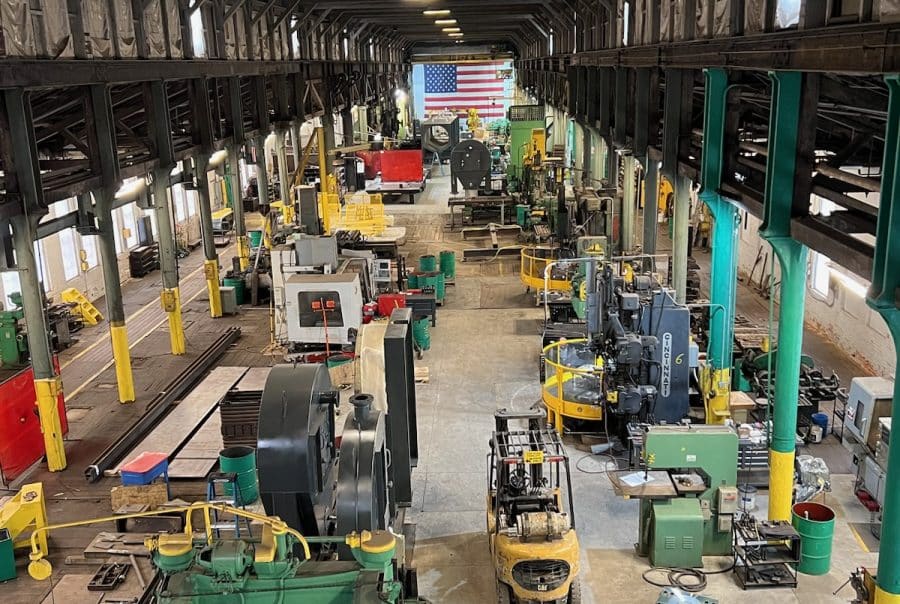
Our facility can manufacture even the largest and most intricate components or systems. Over the last few years, we have made significant investments, totaling hundreds of thousands of dollars to upgrade our facility and equipment. We purchased additional CNC Mills and Lathes as well as vertical and horizontal lathes to expand our capabilities and to have redundant production capabilities that minimizes the impact of equipment downtime! Finch possesses some of the US’s largest vertical and horizontal lathes and a 750-ton Wheel Press machine, one of the largest, that has pressed auger & stone crusher shafts, & the shafts out of the largest Trunnions!

Installing a Rotary Cooler
IN A PINCH, CALL FINCH!
Our skilled machinists, knowledgeable engineers, unique equipment, and customer dedication allow Finch to accommodate urgent requests and emergency work. We will be on a call or videoconference 24/7 or on the road that day to assist our customers in an urgent situation.

15″ Trunnion Assembly
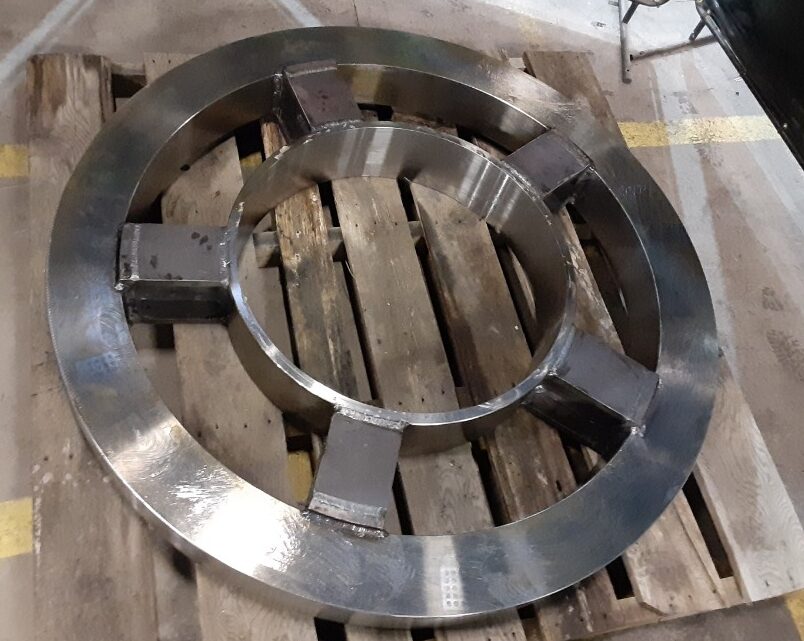
Custom Design Tire for Rotary Calciner
Our suppliers are thoroughly vetted, and we have visited, inspected, and many of them have been partners with us for years. This close relationship ensures quality raw materials and reduces delays related to sourcing. These trusted suppliers are more critical in emergency projects since they will work with us to find the most expedient and cost-effective options.
We recently completed a large emergency replacement project in 8 weeks by finding alternative sourcing for a gear, worked closely with our forging partner, and created a design and install plan that routinely would have taken 24 weeks to manufacture just the gear! Also, we manufactured and shipped a replacement trunnion in 36 hours.

42″ Thrust Roller Assembly

Finch Manufactured Rotary Dryer
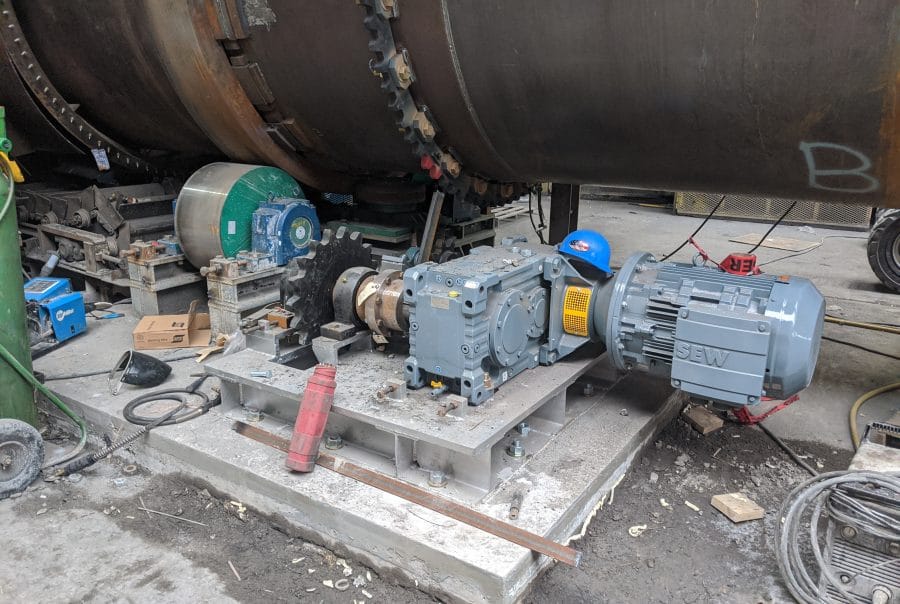
Drive System
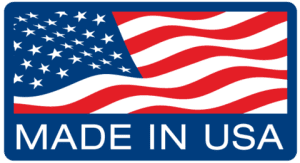
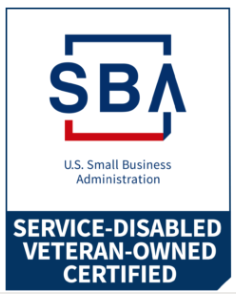
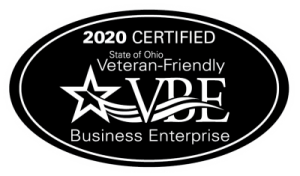
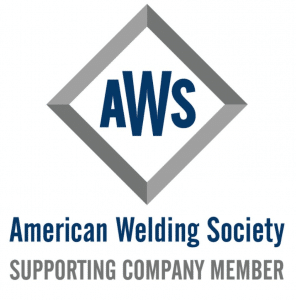
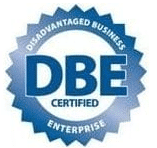